What if you could prevent costly repairs before they happen and keep your facility running at peak efficiency? As a facility manager with over 20 years of experience, I’ve witnessed first-hand how a well-executed preventative maintenance program can be the difference between a smoothly operating building and a constant cycle of breakdowns. When maintenance is proactive rather than reactive, structures stay stronger, energy costs drop, and occupants enjoy safer, more comfortable environments. The key? A strategic approach that maximises efficiency while minimising downtime. Keep reading to discover how preventative maintenance can protect your investment and keep your facility performing at its best.
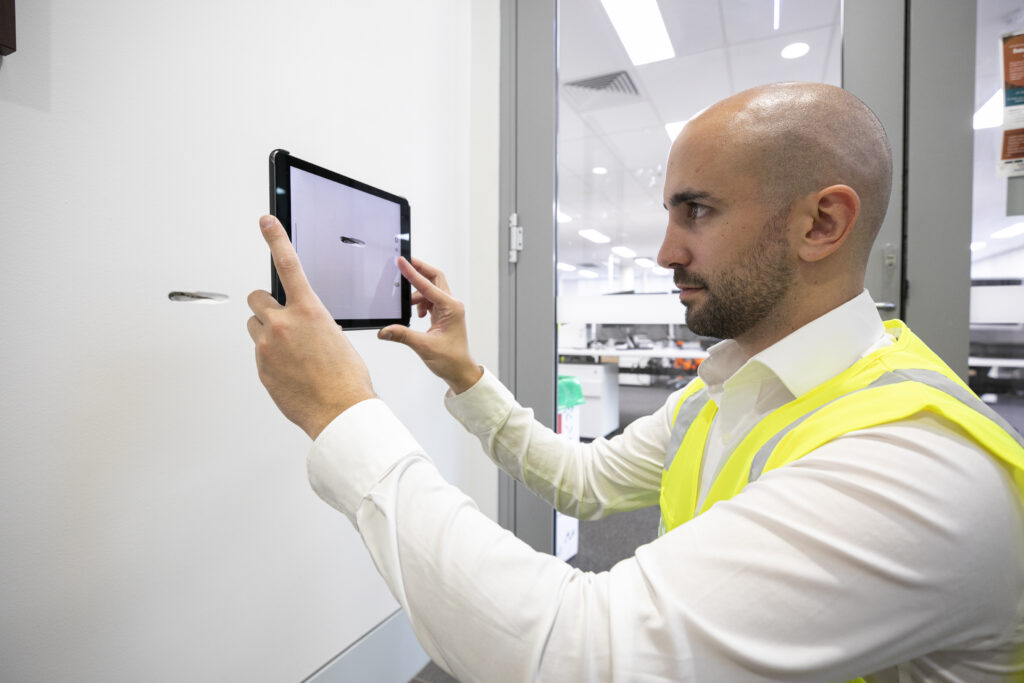
The Value of Preventative Maintenance
Preventative maintenance programs yield significant benefits:
- Reduce unexpected breakdowns by up to 70-80%
- Lower energy costs by 15-20% compared to poorly maintained buildings
- Provide a 545% return on investment over 25 years
- Increase occupancy rates by 15-20%
Many building owners initially view maintenance as a cost to minimize. However, preventative maintenance maximizes the value and longevity of our built environment.
Understanding Preventative Maintenance
Preventative maintenance takes a proactive approach. Instead of waiting for systems to fail, we systematically inspect, clean, and repair building components on a regular schedule.
Theoretical Foundations
Preventative maintenance is rooted in reliability engineering and asset management principles. By understanding typical lifecycles and failure modes of building systems, we can predict maintenance needs and intervene before issues escalate.
A key concept is the P-F curve, which illustrates equipment performance degradation over time. Identifying the point where deterioration becomes detectable (P point) and intervening before functional failure (F point) extends equipment life and avoids costly breakdowns.
Practical Applications
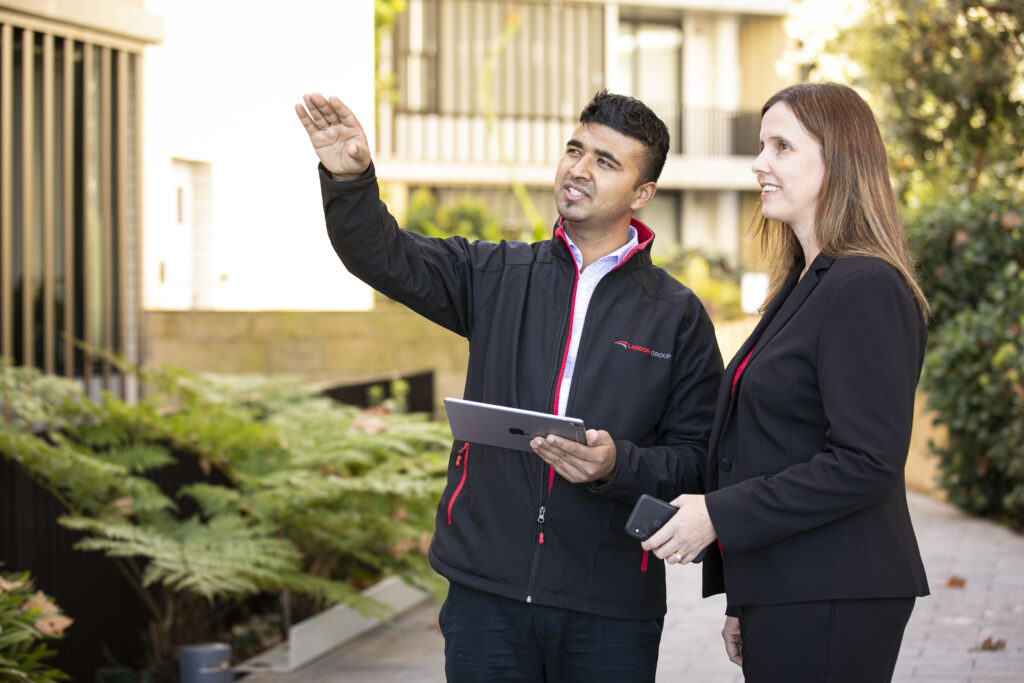
Preventative maintenance encompasses a wide range of activities:
- Regular inspections of building systems (HVAC, electrical, plumbing, etc.)
- Scheduled cleaning and lubrication of equipment
- Replacement of wear items before failure
- Monitoring of key performance indicators
- Analysis of maintenance data to identify trends and improve schedules
In a commercial office building, this might involve quarterly HVAC filter changes, annual roof inspections, and monthly checks of emergency lighting systems.
Overcoming Implementation Challenges
Implementing comprehensive preventative maintenance programs comes with obstacles:
- Budget constraints
- Lack of skilled personnel
- Resistance to change from staff accustomed to reactive maintenance
- Difficulty quantifying ROI
To overcome these challenges, build a strong business case for preventative maintenance. Clearly talk long-term benefits, including reduced operating costs, improved energy efficiency, and increased asset value.
Implementing a Preventative Maintenance Program
Let’s walk through the steps of implementing a preventative maintenance program in your building.
Step 1: Asset Inventory and Assessment
Create a comprehensive inventory of all building systems and components, from major mechanical systems to smaller items like door hardware and light fixtures.
For each asset, document:
- Make and model
- Age and expected lifespan
- Current condition
- Criticality to building operations
Step 2: Develop Maintenance Schedules
Based on manufacturer recommendations, industry best practices, and your experience, create detailed maintenance schedules for each asset. Specify:
- Frequency of inspections and maintenance tasks
- Specific procedures to follow
- Required tools and materials
- Estimated time for completion
Step 3: Implement a CMMS
A Computerised Maintenance Management System (CMMS) is essential for managing complex preventative maintenance programs. This software helps:
- Schedule and track maintenance tasks
- Manage work orders
- Track inventory of spare parts
- Analyse maintenance data and generate reports
Step 4: Train Your Team
Ensure your maintenance staff is fully trained on new procedures and software. This may involve bringing in outside experts or sending staff to specialised training programs.
Step 5: Monitor and Adjust
Once your program is running, continuously monitor it’s effectiveness. Track key metrics:
- Equipment downtime
- Maintenance costs
- Energy consumption
- Occupant comfort and satisfaction
Use this data to refine maintenance schedules and procedures over time.
Common Pitfalls and How to Avoid Them
Even with careful planning, several pitfalls can derail a preventative maintenance program:
Over-maintenance
While proactivity is important, excessive maintenance can reduce equipment lifespan and waste resources. Strike a balance by basing maintenance schedules on data and manufacturer recommendations.
Neglecting Root Cause Analysis
When issues arise, don’t just fix the immediate problem. Take time to identify and address the root cause to prevent recurrence.
Failing to Update Procedures
As equipment ages and building usage changes, maintenance procedures need to evolve. Regularly review and update your maintenance plans.
Ignoring Predictive Maintenance Opportunities
While scheduled maintenance is important, don’t overlook the potential of predictive maintenance techniques, such as vibration analysis or infrared thermography, to further improve your program.
Adapting to Different Scenarios
Every building is unique, and your preventative maintenance program should reflect that. Here are tips for adapting your approach to different scenarios:
Historic Buildings
Focus on preserving original materials and features while meeting modern performance standards. This may involve:
- Specialized cleaning techniques for delicate surfaces
- Careful integration of modern systems with historic architecture
- Regular inspections for moisture intrusion and structural issues
- Collaboration with preservation experts for major repairs
High-rise Buildings
Pay special attention to vertical transportation systems and façade maintenance. Key considerations include:
- Regular elevator and escalator maintenance to ensure safety and reliability
- Façade inspections and repairs to prevent falling debris hazards
- Robust fire safety systems and evacuation procedures
- Efficient waste management and vertical logistics
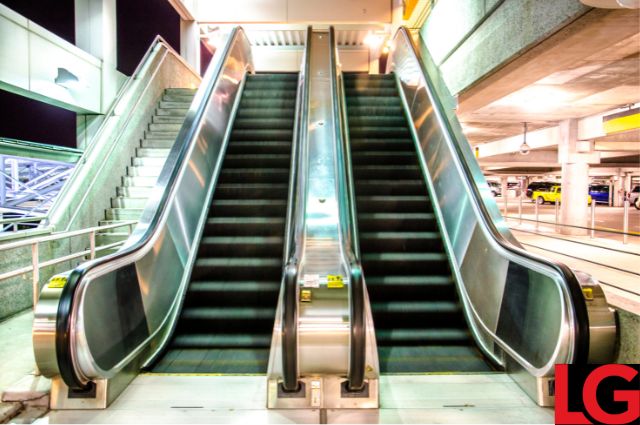
Healthcare Facilities
Prioritize infection control and compliance with stringent regulatory requirements. This involves:
- Frequent cleaning and disinfection of high-touch surfaces
- Maintenance of specialized medical equipment
- Strict air quality control and filtration
- Regular testing of backup power systems
Data Centres
Emphasize redundancy and uninterrupted operation of critical systems. Focus on:
- Maintaining precise temperature and humidity control
- Regular testing and maintenance of UPS systems and generators
- Proactive replacement of critical components before failure
- Robust cybersecurity measures for building management systems
Frequently Asked Questions
What is preventative maintenance in buildings?
Preventative maintenance in buildings involves regularly scheduled inspections, cleaning, and repairs of building systems and components to prevent breakdowns and extend their lifespan.
How often should preventative maintenance be performed?
The frequency of preventative maintenance depends on the specific equipment and it’s usage. Some tasks may be daily or weekly, while others are monthly, quarterly, or annual. Manufacturer recommendations and industry standards provide guidance.
What are the benefits of preventative maintenance?
Preventative maintenance reduces unexpected breakdowns, lowers energy costs, extends equipment life, improves occupant comfort, and can provide significant return on investment over time.
How do I create a preventative maintenance schedule?
To create a preventative maintenance schedule, start by inventorying all building assets, researching manufacturer recommendations, considering usage patterns, and balancing resource constraints.
Can preventative maintenance reduce energy costs?
Yes, well-maintained equipment operates more efficiently, reducing energy consumption. Regular maintenance of HVAC systems, for example, can significantly lower energy bills.
How does preventative maintenance impact building value?
Preventative maintenance preserves building condition, extends equipment life, and reduces operating costs, all of which contribute to higher property values and improved marketability.
What are common mistakes in preventative maintenance programs?
Common mistakes include over-maintenance, neglecting root cause analysis, failing to update procedures, and ignoring opportunities for predictive maintenance techniques.
Key Takeaways
- Preventative maintenance significantly reduces costs, improves building performance, and extends asset life.
- Successful implementation needs careful planning, suitable tools, and ongoing commitment.
- Regular monitoring and adjustment improve programs over time.
- Adapting approaches to specific building needs maximizes preventative maintenance benefits.
Speak to Landon Group today and we can understand your preventative maintenance program needs, regardless of the premise or business you operate.
Keep Your Facility at Its Best
Looking to stay ahead in maintaining exceptional facilities? Explore these related resources:
–9 Signs of an Excellent Commercial Cleaner – Spot the traits that separate the good from the great.
–Factory and Warehouse Cleaning Techniques – Learn the secrets to tackling even the toughest industrial cleaning challenges.
–Top Preventative Property Management Actions for Facilities Managers – Discover proactive steps to keep your property in top shape.
These blogs are filled with actionable insights to help you make informed choices and uphold the highest standards for your facility. Dive in today!